According to the 2022-2023 Global Risks Perception Survey (GRPS), an “Energy supply crisis” is among the top risks for 2023 with the greatest potential global impact.
Understanding the Energy Crisis in 2023
Due to Russia’s invasion of Ukraine, oil and gas prices have reached their highest levels in nearly a decade. As a major consumer of energy, the manufacturing industry is particularly vulnerable to the current energy crisis.
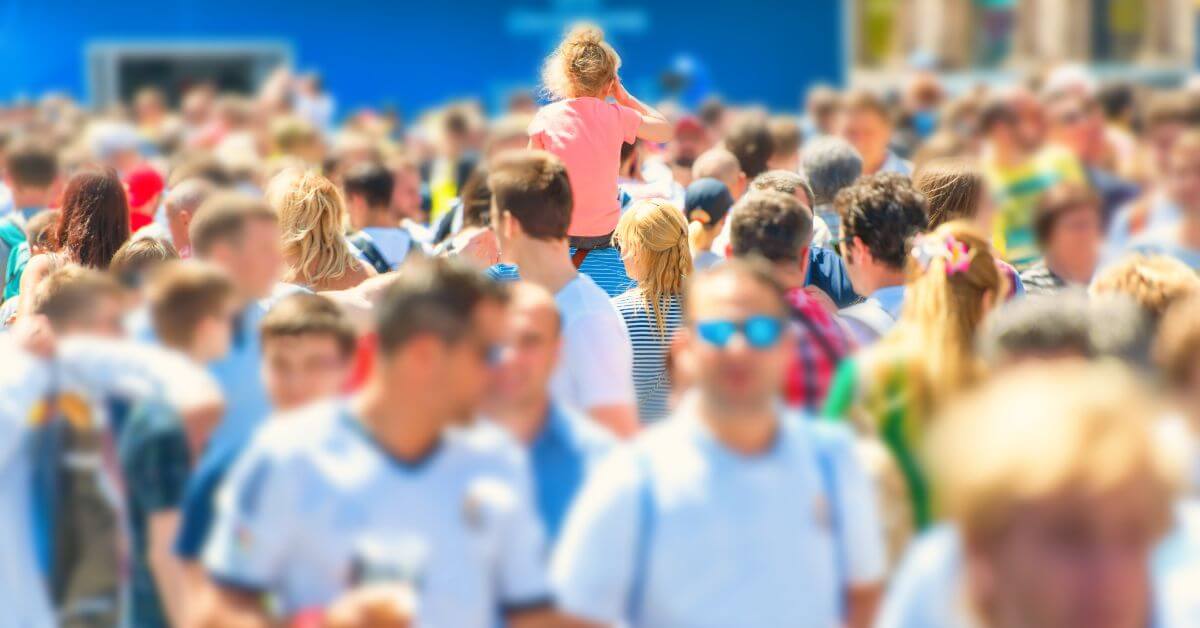
Causes of the energy crisis
There are several causes of the energy crisis. In addition to the war in Ukraine, there are several other causes of the energy crisis.
Some of the main causes include:
- Overconsumption: The energy crisis is a result of many different strains on our natural resources, not just one.
- Overpopulation: As the global population continues to grow, so does the demand for energy.
- Wastage of Energy: Energy is often wasted through inefficient use or poor distribution systems.
- Major Accidents and Natural Calamities: Accidents and natural calamities can disrupt energy supply.
- Increase in demand for natural gas and coal:As countries emerged from Covid lockdowns, industries started using much more natural gas. Coal prices have also risen sharply – tripling over the past year.
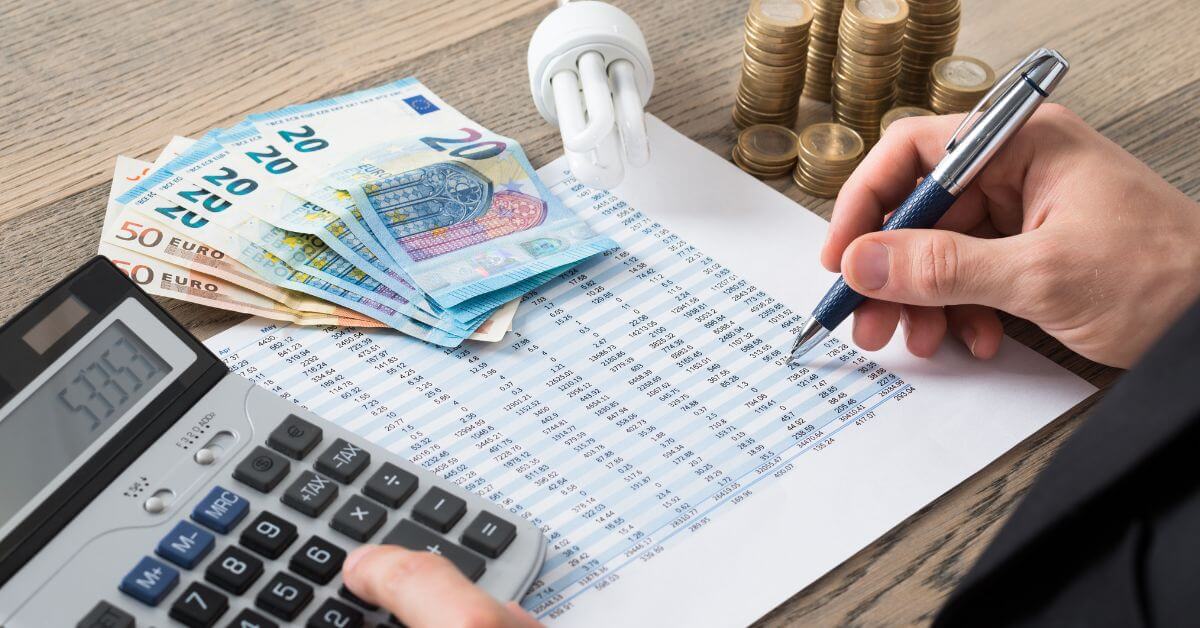
How does it Effects on the Die Casting Industry?
Higher energy costs
The energy crisis has led to an increase in the cost of energy. This can increase the cost of production for industries that rely on energy-intensive processes.
Reduced Production Capacity and Increased Costs
Higher energy costs can lead to reduced production capacity for industries that rely on energy-intensive processes. This is because it may become too expensive to continue operating at full capacity.
Strategies for Energy Efficiency in Die Casting Operations
There are several strategies that can be used to improve energy efficiency in die casting operations.
Use of renewable energy sources
One way to reduce the carbon footprint of die casting operations is to use renewable energy sources such as solar or wind power. This can help to reduce the reliance on non-renewable energy sources such as coal and natural gas.
Adoption of energy-efficient equipment and processes
Another way to improve energy efficiency in die casting operations is to adopt energy-efficient equipment and processes.
Optimizing production schedules to reduce energy consumption
Optimizing production schedules can help to reduce energy consumption in die casting operations. Also, scheduling production in a way that minimizes downtime and maximizes efficiency can also help to reduce energy consumption.
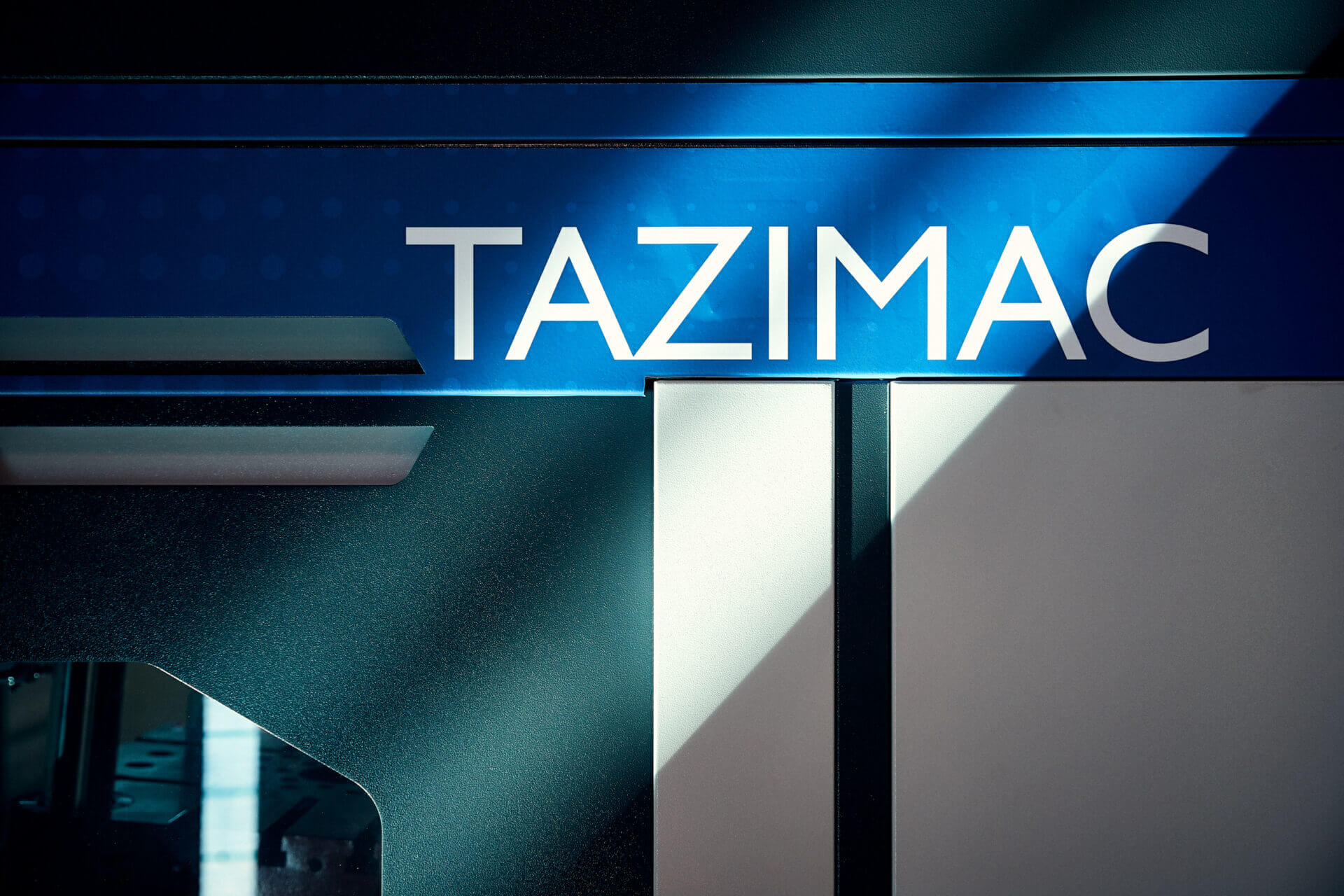
TAZIMAC Servo- Hydraulic Energy-Saving System
Our servo system can save 35% more energy than the original die-casting machine during operation, and 45% more after automation!
Read more:TAZIMAC ZINC HOT CHAMBER DIE CASTING MACHINE
Learn about how this innovative equipment to reduce your carbon footprint and save electricity in the process:
INNOVATIONS IN ZINC HOT CHAMBER DIE CASTING EQUIPMENT THAT REDUCE CARBON FOOTPRINT