I. How MES Optimizes Die Casting Production Processes
Manufacturing Execution Systems (MES) bring numerous benefits to the die casting industry, optimizing crucial production processes and enhancing overall manufacturing efficiency.
A. Die Casting Process Control and Monitoring
- Precision in Process Parameters: According to Wiki, MES enables meticulous regulation of key parameters like temperature, injection speed, and pressure, which are paramount for high-quality castings. Consistent control translates to reduced variability, ensuring each product meets stringent standards.
- Real-time Adjustments: Real-time monitoring empowers manufacturers to make immediate corrections based on sensor feedback, significantly reducing downtime and waste.
B. Real-time Data Collection and Visualization
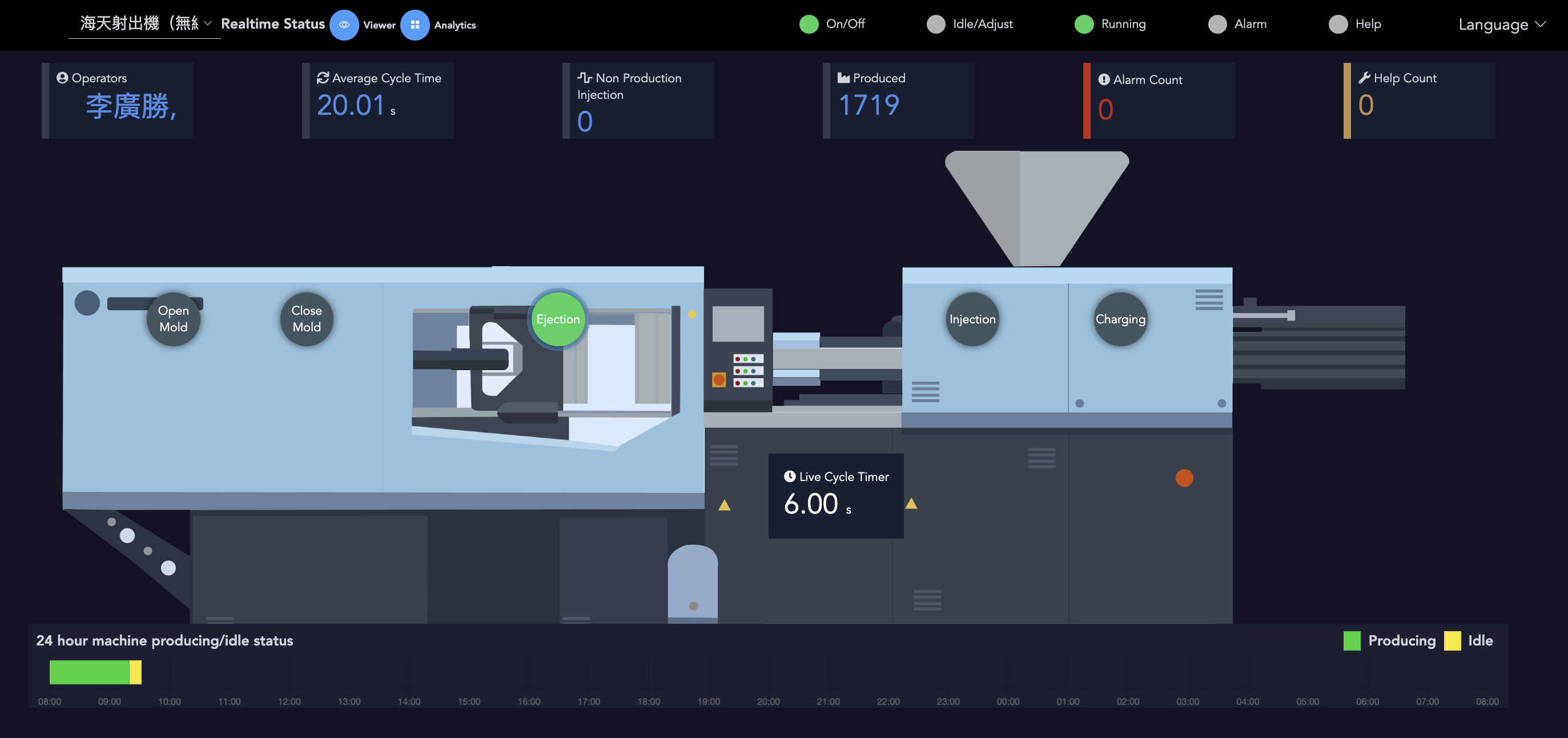
- Continuous Data Streams: MES collects extensive data from machines and sensors, offering a holistic view of the production process. Platform capabilities from Fiix Software illustrate effective data integration, ensuring accuracy.
- Visualization Tools: Sophisticated dashboards and reports present real-time Key Performance Indicators (KPIs), allowing for prompt identification and management of issues before they escalate (Sw Siemens).
C. Automated Process Routing Management
- Dynamic Scheduling: MES dynamically adjusts schedules based on real-time insights, enhancing resource utilization and minimizing bottlenecks (UpKeep).
- Workflow Automation: MES minimizes manual interventions by automating workflows, boosting efficiency, and reducing error rates.
Interested in how the zinc die casting process can benefit from MES?
Contact us now: https://www.tazimac.com/en/contact-us/
II. MES Applications for Improved Zinc Die Casting Quality Management
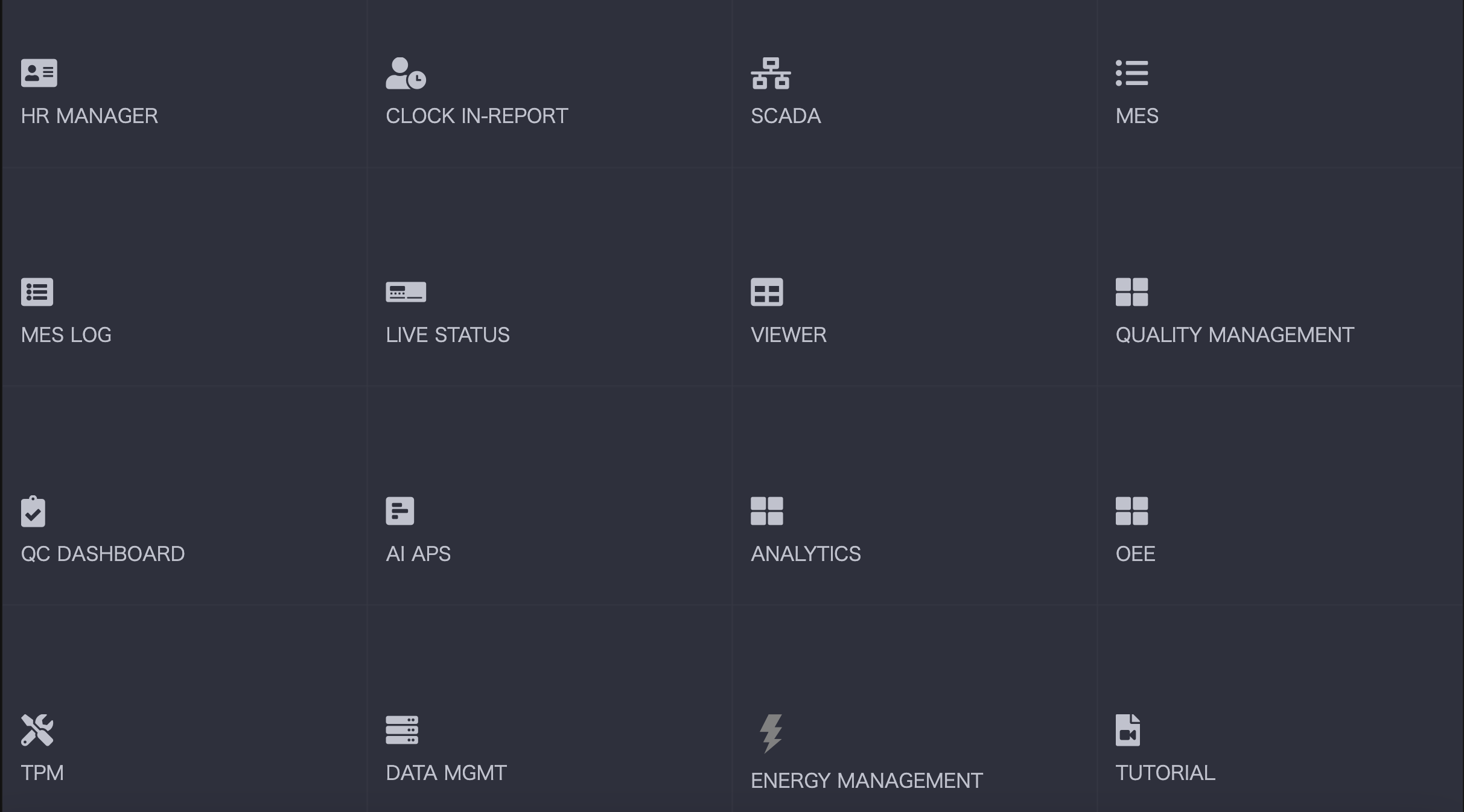
Enhanced quality management achievable through MES implementation ensures product reliability and conformity to high standards.
A. Defect Tracking and Analysis
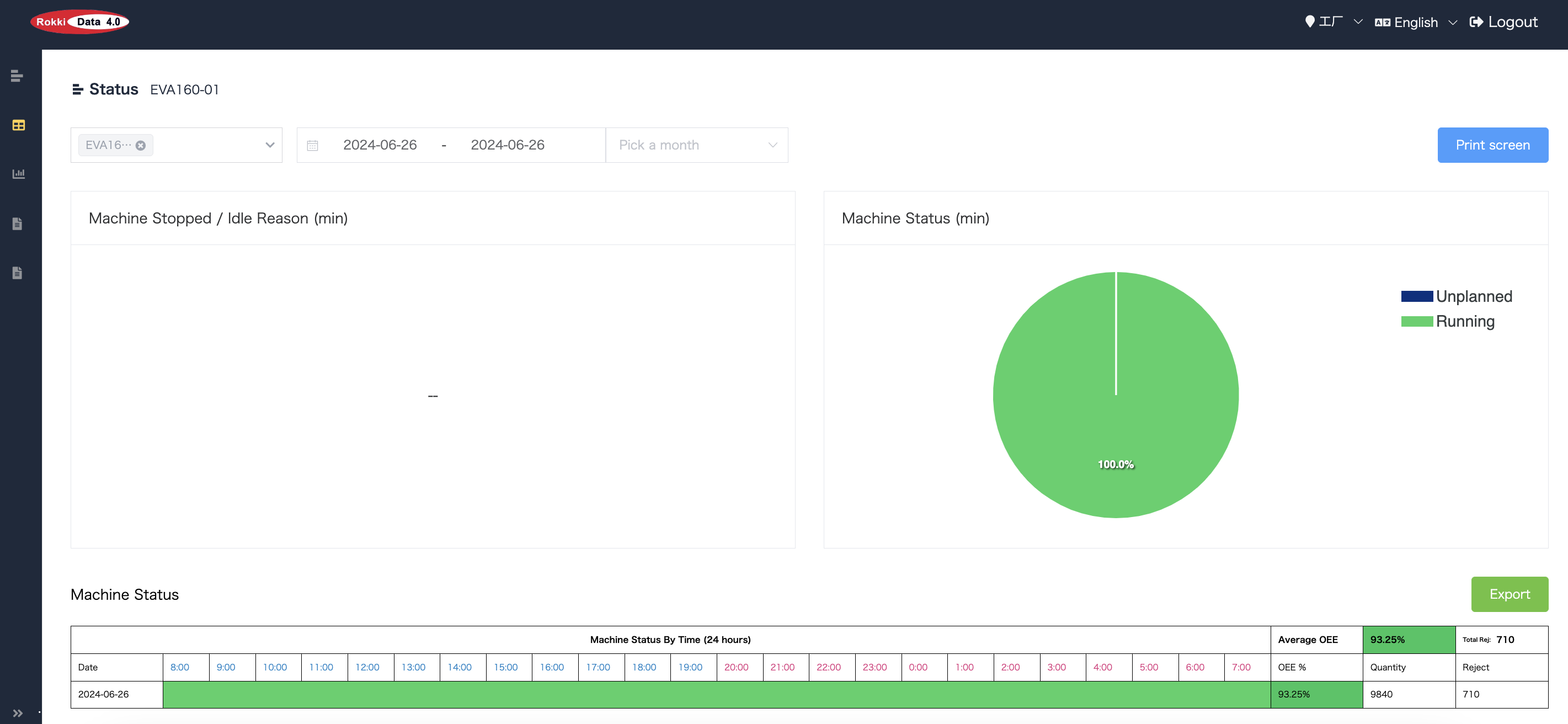
- In-depth Defect Tracking: MES systems can track defects in real-time, providing immediate identification and remedy.
- Root Cause Analysis: Advanced MES functionalities facilitate in-depth root cause analysis, helping uncover and resolve root issues promptly.
B. Statistical Process Control (SPC) Applications
- Real-time SPC: As highlighted by various sources, MES incorporates SPC to monitor and regulate quality in real-time, minimizing deviation and enhancing product consistency.
- Automated Sampling and Analysis: MES can automate sampling and statistical analysis, ensuring standards are consistently met and quality is preserved.
C. Quality Data Reporting and Analysis
- Comprehensive Reporting: MES generates detailed reports supporting compliance and continuous improvement efforts.
- Data-Driven Insights: The data derived from MES systems can be analyzed comprehensively, yielding insights that underpin strategic decisions.
III. MES-based Die Casting Equipment Maintenance Management

A. Preventive Maintenance Planning and Execution
- Scheduled Maintenance: MES assists with planning and scheduling regular maintenance, reducing unexpected downtimes.
- Maintenance Alerts: Automated alerts ensure the timely execution of maintenance activities, preventing delays.
B. Failure Diagnosis and Repair Management
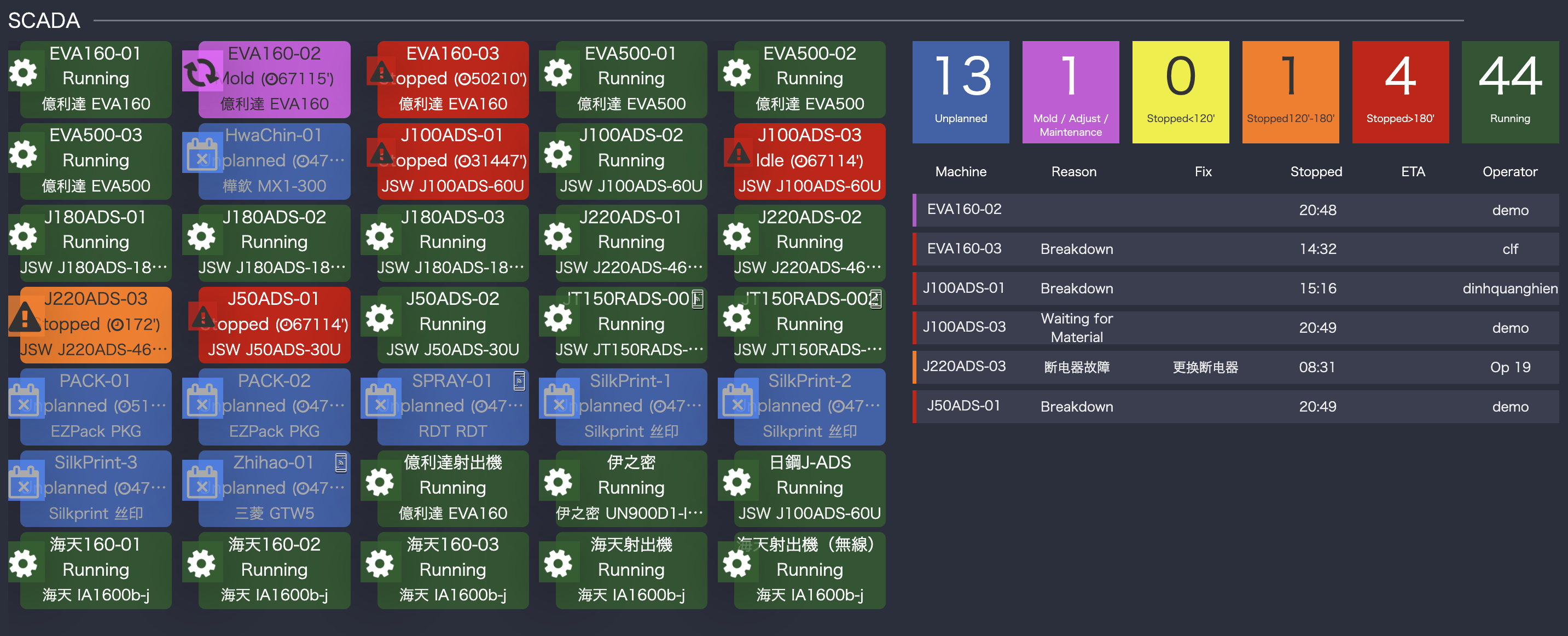
C. Spare Parts Inventory and Procurement Optimization
- Inventory Management: MES optimizes spare parts inventory, ensuring essential components are readily available.
- Procurement Efficiency: Streamlined procurement processes reduce lead times and associated costs.
IV. Digital Die Casting Plant: MES and Smart Manufacturing
A. Production Visualization and Bottleneck Analysis
- Real-time Visualization: MES provides real-time visualization of the production process to identify and resolve bottlenecks efficiently, as explained by Buhler.
- Bottleneck Analysis: In-depth analysis of production bottlenecks leads to improved manufacturing flow.
B. Machine Learning Applications in Die Casting
- Predictive Analytics: MES incorporates machine learning algorithms to foresee and mitigate potential issues. Examples provided by JIN Energy illustrate these applications.
- Continuous Improvement: Machine learning within MES enables learning from historical data, driving continuous enhancements.
C. Data-Driven Manufacturing Decision Support
- Intelligent Decision Support: MES systems offer data-driven decision support by analyzing vast production data and generating actionable insights.
- Enhanced Collaboration: Centralized data exchange on MES platforms fosters better collaboration across departments.
V. Integrated MES for End-to-End Die Casting Quality Control
A. Raw Material Quality Traceability
- Complete Traceability: MES tracks raw materials from entry to finished goods, ensuring comprehensive traceability.
- Supplier Quality Management: Monitoring and managing supplier quality reduces defects, enhancing production integrity.
B. In-Process Quality Monitoring and Analysis
- Real-time Monitoring: Continuous monitoring of in-process materials ensures compliance with specifications.
- In-depth Analysis: Real-time data analysis facilitates timely corrective actions.
C. Product Quality Inspection and Digital Footprint
- Automated Inspections: MES automates inspections to ensure consistent quality, reducing manual errors.
- Digital Footprint: MES creates a digital footprint for all production stages, aiding in traceability and quality assurance.
Conclusion
Adopting an MES can revolutionize die casting production, bringing benefits in process control, quality management, equipment maintenance, digital transformation, and complete quality control. For die-casting companies aiming to thrive, MES is not just an advantage but a necessity to ensure long-term success.
Embrace MES technology for transformative advancements in your manufacturing processes, staying ahead in the competitive die casting industry.
The integration of MES into die casting operations ensures improved efficiency, reduced costs, enhanced product quality, and fortified regulatory compliance.
Read more: What is a manufacturing execution system (MES)?
Interested in how the zinc die casting process can benefit from MES?
Contact us now: https://www.tazimac.com/en/contact-us/