Zinc die casting is a manufacturing process that involves the creation of intricate metal parts through the use of zinc alloys. It has become a popular method for producing high-quality metal parts with tight tolerances and complex geometries.
In this blog post, we will explore the principles, benefits, and applications of zinc die casting.
What is Zinc Die Casting?
Zinc die casting is a metal casting process that involves injecting molten zinc alloy into a steel mold to create complex shapes. The molten metal is injected at high pressure into the mold, where it solidifies and takes the mold cavity shape.
The resulting parts have a smooth surface finish and can be produced in high volumes with little to no post-processing.
The three most important pieces of information about zinc die casting are:
- Zinc die casting is a versatile manufacturing process that can produce complex parts with high precision.
- Zinc die casting is suitable for producing high-volume parts due to its speed and efficiency.
- Zinc die casting offers a range of advantages over other casting processes, including superior surface finish, dimensional stability, and the ability to produce thin-walled parts.
Zinc Alloy Characteristics
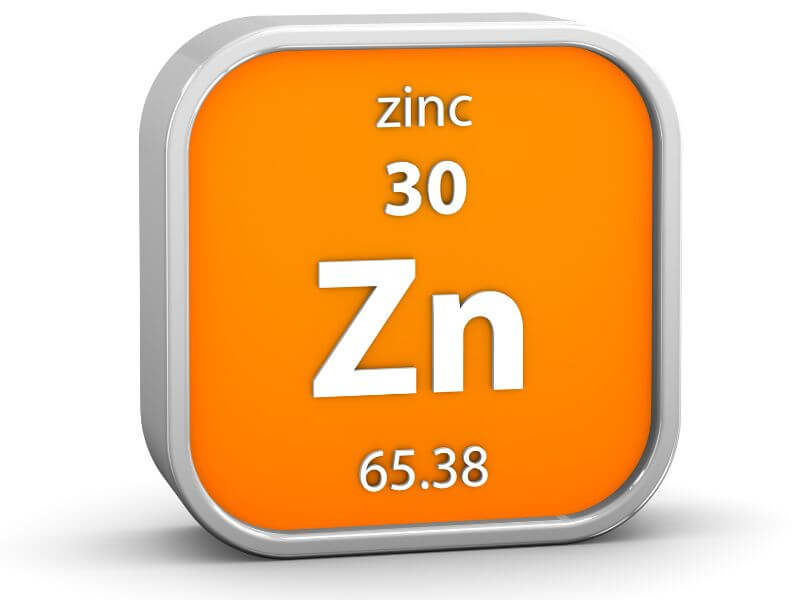
- High strength
- Excellent durability
- Low melting point
- Good fluidity
- Excellent corrosion resistance
- Easy to cast
- Low density
- Relatively low cost compared to other metals
Highly ductile and have excellent casting properties, which make them an ideal material for die casting.
Zinc alloys are also highly recyclable, making them an environmentally friendly choice for manufacturers.
What is the Zinc Die Casting Process?
Zinc die casting is a manufacturing process used to make parts out of zinc alloy. The process starts by making a mold of the part you want to produce. This mold is made out of steel and is designed to the exact specifications of the part.
The mold is then mounted onto a die-casting machine, which heats the mold to a specific temperature. The molten zinc alloy is then injected into the mold under high pressure, where it solidifies and takes the shape of the mold cavity.
This process can be done using a hot chamber machine, where the melting pot is immersed in the molten metal, or a cold chamber machine, where the molten metal is transported to the injection chamber using a ladle.
Once the part has cooled and solidified, it is removed from the mold and can be post-processed as needed. This may include cleaning, trimming, or machining to refine the part’s final shape.
Zinc die casting is commonly used to make parts for automobiles, electronics, and other consumer goods due to its ability to produce intricate parts with high accuracy and repeatability.
Read more:Our One-Stop Services
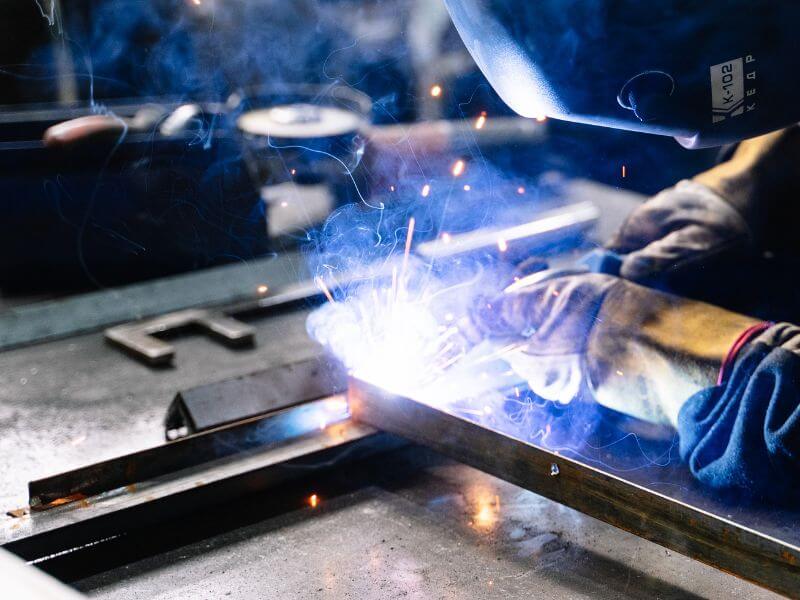
Advantages of Zinc Die Casting
Zinc die casting offers several advantages over other manufacturing methods, including:
- High dimensional accuracy
- Excellent surface finish
- High production volumes
- Low production costs
- The ability to produce complex shapes and geometries
- Good strength and durability
- Resistance to corrosion
- High recyclability
Applications of Zinc Die Casts
Zinc die casts are used in a wide range of applications, including automotive, electrical, and consumer products.
Some common applications of zinc die casts include:
- Automotive parts, such as transmission housings and engine blocks
- Electrical components, such as connectors and switchgear
- Consumer products, such as door handles, faucets, and locks
- Medical equipment, such as surgical instruments and prosthetics
- Aerospace and defense applications, such as missile components and aircraft parts
Conclusion
In conclusion, zinc dies casting is a versatile and cost-effective manufacturing process that offers many benefits over other methods.
Its excellent surface finish, dimensional accuracy, and ability to produce complex shapes make it an ideal choice for a wide range of applications. As a highly recyclable and environmentally friendly material, zinc alloys also offer an attractive option for manufacturers looking to reduce their carbon footprint.